In the fast-paced world, every consumer wants their ordered product delivered at faster rates without any delays. In most industries, manufacturing processes can be optimizing packaging factory workflows for increased efficiency so that would not cause any delays. Even in manufacturing, packaging plays an important role. The packaging industry faces challenges and one of them is to maintain lead times. Well, a business or brand can find a packaging factory that provides optimized packaging solutions through Maker’s Row, an online platform that connects reliable and capable manufacturers that can streamline the production process efficiently.
Lead time is about the time it takes to produce and deliver packaging from the initial order to the final product ready for delivery. Long lead times result in delays and customer dissatisfaction too. They need to follow multiple strategies to optimize the lead process. So improving the speed of packaging production is not only essential for staying competitive but also helps in optimizing packaging factory workflows for increased efficiency and increases profitability as well.
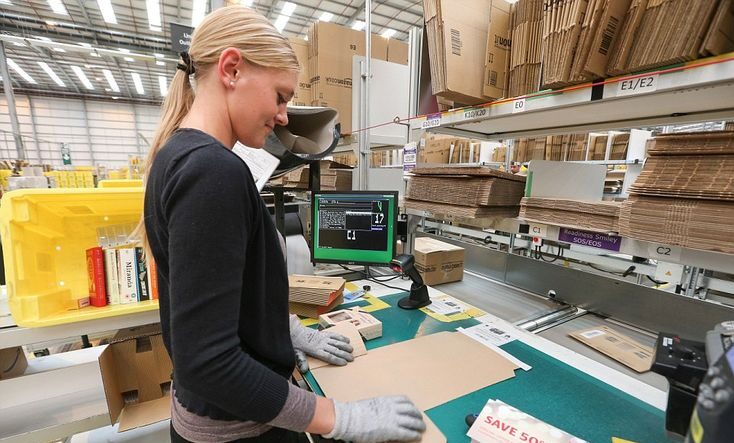
image credit: pinterest
Key strategies for reducing lead times in packaging production
1. Streamline Workflow And Processes
For optimizing packaging factory workflows for increased efficiency, they need to map out the entire production process first. Then they need to identify the inefficiencies or hurdles that might come across. By clearly understanding the steps involved in the packaging process, the factory can note the areas that require improvement. They can implement standardised procedures across all stages of production to ensure all workers follow best practices.
This helps in reducing errors and delays in production lead times. Adopt the lean manufacturing principle to minimize waste and optimize the use of resources. There are techniques like just-in-time production that help to avoid overproduction.
2. Invest In Automation And Technology
Packaging factories can integrate innovative and automated systems in areas such as printing, cutting, and packaging assembly. This can significantly reduce manual labor time and errors and speed up the production process. There is software available that helps to track inventory, production schedules, and order processing. Real-time data helps with quick decision-making and better coordination.
Computer-aided design and computer-aided manufacturing technologies can speed up product designing and prototyping. This helps in increasing accuracy levels and reducing rework, along with optimizing packaging factory workflows for increased efficiency.
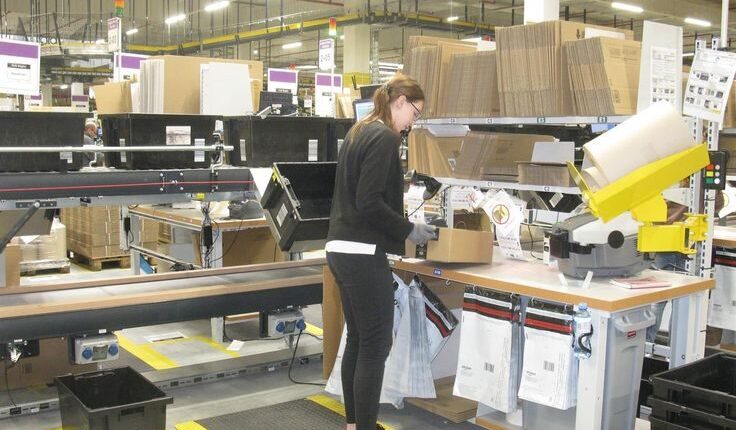
image credit: pinterest
3. Optimize Supply Chain Management
Building strong relationships with key suppliers helps in optimizing packaging factory workflows for increased efficiency and quicker response times with prioritization of your orders. This can include a favorable terms negotiation. They need to also ensure suppliers have reliable stock. An efficient inventory management system can ensure that the right materials are available at the right time and no delay occurs at the end. This helps in reducing lead times in packaging processes.
4. Improve Communication And Collaboration
They should encourage better communication between the designs, production, and logistics teams. This helps streamline the design-making process and resolve issues quickly. Clear and constant communication with customers regarding lead time expectations and progress can prevent misunderstandings and allow for better planning.
For optimizing packaging factory workflows for increased efficiency, they can implement real-time production tracking and monitoring tools. It helps to spot potential problems and delays before they occur and create problems and immediate corrective actions.
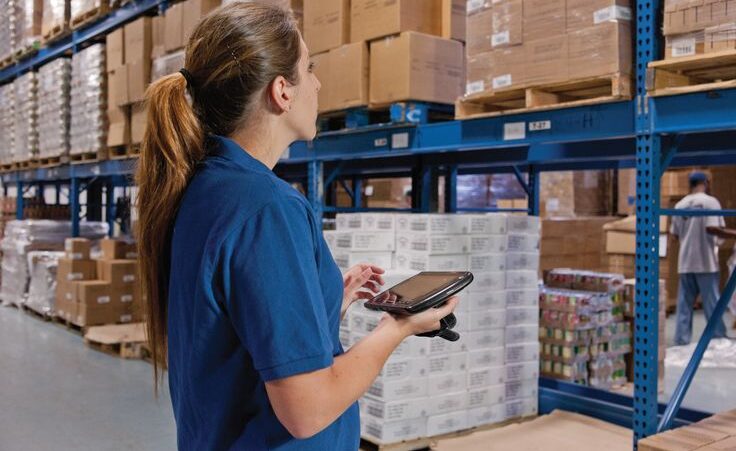
image credit: pinterest
5. Flexibility In Production Scheduling
Implementing flexible scheduling practices allows optimizing packaging factory workflows for increased efficiency. Also manufacturers to quickly adjust and change to customer demand and special requests. They should develop systems for quickly identifying high-priority orders and fast-tracking them without disrupting production flow. Adjust working shifts and production schedules to meet increased demand, ensuring production runs smoothly while reducing lead times in packaging production processes.
6. Continuous Improvement And Employee Training
For optimizing packaging factory workflows for increased efficiency, they need to build a culture of continuous improvement. They should encourage employees to suggest and implement process improvements. Small changes can accumulate to reduce lead times significantly. Well-trained staff are more efficient as they make fewer mistakes and are better able to solve issues that cause delay.
Regular training in both technical and process improvement techniques and following quality control procedures helps in reducing lead times in packaging production processes.
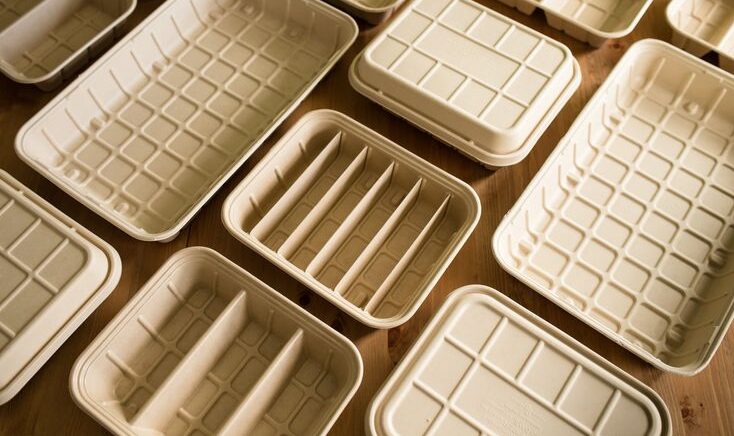
image credit: pinterest
7. Use Of 3D Prototyping And Virtual Testing
Using 3D printing and virtual testing can help in optimizing packaging factory workflows for increased efficiency. It brings development in packaging, designing, and allowing faster changes and adjustments. This is possible before physical and actual production begins. Quick prototyping tools help to reduce the time spent on testing and adjustments. This technique enables faster approval of the quality department. That gives a signal to move forward for the next step quickly while reducing lead times in packaging production processes.
8. Data-Driven Decision Making
Factories need to leverage predictive analytics to understand the forecast demand more effectively and accurately. This helps in optimizing packaging factory workflows for increased efficiency and management. So it helps in avoiding unnecessary delays that get caused usually in production processes. Monitor key performance indicators in packaging production, such as cycle time and on-time delivery defect rates, to identify errors for improvement and ensure that the production process remains efficient.
Integrating OCR API with data analytics tools can further enhance decision-making by automatically extracting and analyzing data from physical documents, such as shipping labels, quality control reports, and supplier invoices.
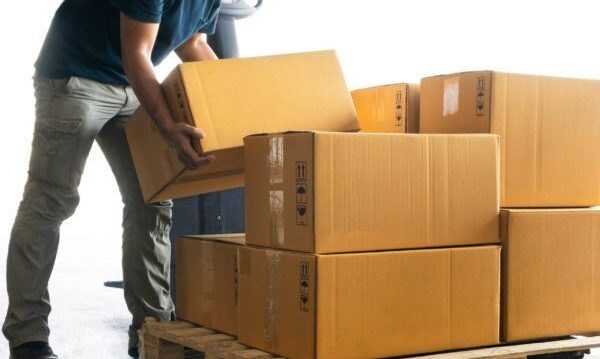
image credit: pinterest
How Maker’s Row helps in finding packaging factories that optimize production
Brands and businesses usually face difficulties and it is a time-consuming process to find packaging factories that provide optimized solutions and no delays in packaging production. Maker’s Row is a platform that makes it possible by connecting brands and manufacturers according to their requirements, including from the packaging industry. The platform aims to streamline the process and offers help in the following ways:
→ If a manufacturer has signed in and has created a profile on Maker’s Row, it automatically lists them in the manufacturers list. The platform provides access to brands for finding the right factory and reliable manufacturers that are capable of providing optimized packaging production.
→ The platform allows brands to filter and find factories based on various criteria, such as production capabilities, expertise in packaging types or materials being used in packaging production. They can also compare and then decide the right factory by going through their profile and present with information such as past work, portfolio, and client reviews too.
→ It also provides access to direct communication between brands and packaging factories, allowing them to discuss timelines, lead times, and production schedules. This helps in better collaboration and clarity between brands and factories.
→ Maker’s Row also offers industry expert advice and informative resources that give insights about the packaging industry and help to understand the production process and optimization strategies, which help factories to grow and improve their quality to produce packaging solutions.
Conclusion
Hence, reducing lead times in packaging production processes requires an efficient approach that integrates process optimization and technology adoption to improve the process. By focusing on streamlining the workflow and investing in automation, packaging factories can achieve a significant reduction in lead times. So all these strategies not only help in optimizing packaging factory workflows for increased efficiency but also improve customer satisfaction, cost savings, and become stronger competition in the packaging industry.
You Can Also Read..