Packaging plays an important role in protecting products, ensuring safety, and enhancing the overall aesthetics of packaged products. Like any other industry, quality control is an integral part of the production process. Packaging factory quality control procedures and best practices need to be followed to execute seamless production. Ensuring quality control in packaging production not only guarantees safety and functionality but also enhances customer satisfaction.
To find packaging factories that are capable of quality production, Maker’s Row is the solution. It is an online platform that helps in collaborating brands with factories that are efficient enough in quality packaging.The efficiency and reliability of packaging depend highly on effective quality control procedures. It helps to meet quality standards and maintain industry regulations too. A consistent packaging factory quality control procedure and best practices helps in preventing many errors.
Here Are Best Practices For Ensuring Quality Control In Packaging Production
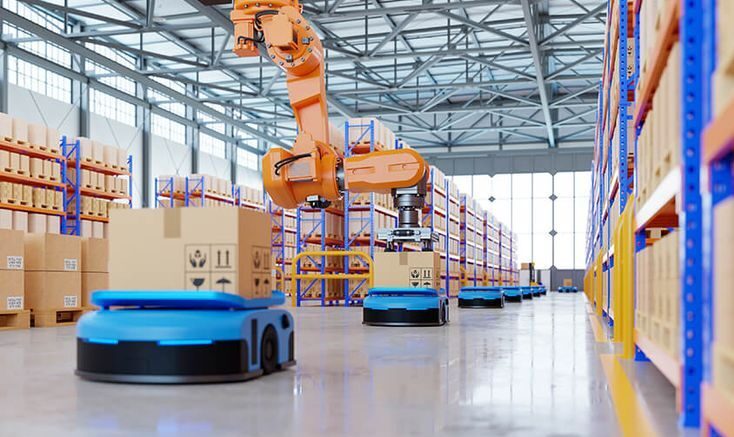
image credit: pinterest
1. Develop A Clear Quality Control Plan
The packaging factory quality control procedures and best practices include how they should define the standards clearly. They should establish clear quality specifications for packaging materials such as strength, durability, dimensions, and visual appearance too. They should create detailed documentation that outlines the quality control procedures consistent throughout the production processes. Maintaining compliance and regulations is also important. They need to ensure that packaging meets and follows the regulatory standards, which are usually different from each other and varied from industry to industry.
2. Select High Quality Materials
Packaging factory quality control procedures and best practices also states how factories should conduct tests of materials that are going to be used. It can be the strength, durability, and suitability of materials, for example, cardboard, plastic, or glass, before using them for production. They should work with trusted suppliers that are consistent with sourcing high-quality materials. They can verify the materials before actual production begins. If the factory provides eco-friendly products, then they should make sure to use materials that are sustainable and eco-friendly without compromising on quality.
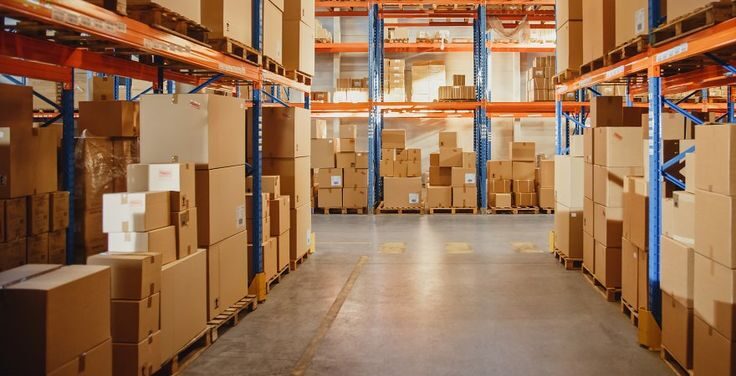
image credit: pinterest
3. Implement Automated Systems
They can implement packaging factory quality control procedures and best practices that state automated systems that help in visual inspection with cameras and sensors. This can detect defects and errors such as misprints, color inconsistencies, or any damaged portion in packaging. Packaging factories should use machines that can check for levels of weight consistency to ensure the products are packaged correctly. It is to check and ensure that the packaging can hold the product’s weight. This helps to solve the query and answers how packaging factories ensure quality control in production.
4. Conduct Regular Quality Audits
They should conduct routine inspections during different stages of packaging production, for example, material preparation, printing, assembly, or sealing, to identify any errors or issues easily. They can also take random samples from batches for in-depth inspection of various quality aspects. It can be related to seal, labeling, or durability accuracy. They should maintain and keep records of audit results to identify trends and improvements. They should address the issues recurring on a regular basis too so packaging factory quality control procedures and best practices can be executed.
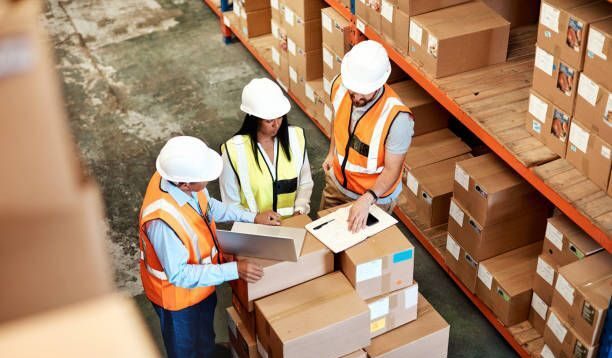
image credit: pinterest
5. Train And Educate Employees
They should ensure that all employees involved in the packaging process are trained and are skilled to understand packaging factory quality control procedures and best practices. They can provide regular training sessions to keep the staff updated on new technologies introduced, industry regulations, and improved quality control methods. They can also involve and encourage workers to report issues and suggest improvements, if any. This helps to clear doubts about how packaging factories ensure quality control in production and leads to continuous improvement.
6. Perform Testing And Validation
For packaging factory quality control procedures and best practices, they can conduct tests such as drop tests, compression tests, or transportation stimulation to ensure that the packaging can withstand handling, transportation, and environmental conditions. They need to check shelf life testing for food and pharamacutical packaging. Testing packaging materials under various conditions can help to understand and ensure product freshness and integrity over time. They can obtain consumer feedback regarding packaging durability and design, ensuring the packaging meets their expectations.
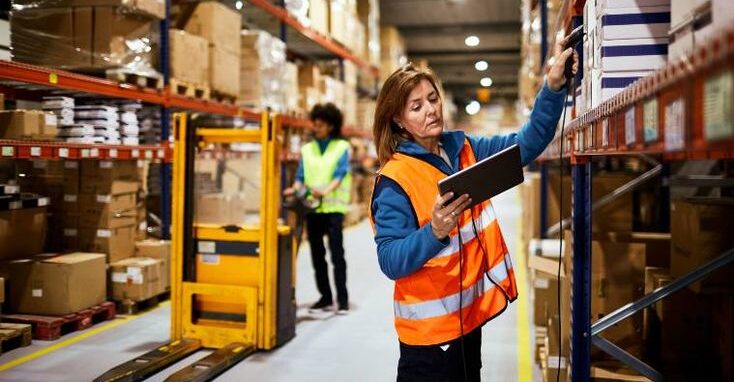
image credit: pinterest
7. Establish Traceability And Tracking Systems
To decline the doubts about how packaging factories ensure quality control in production, factories need to implement systems that track and trace every packaging batch from raw materials used to the final product. This ensures the ability and accountability to address potential issues quickly. They should maintain all the accurate records from previous stages of production and inspections, all the corrective actions taken for its improvement and all test results too. This information is valuable for audits and the continuous improvement process.
8. Final Inspection And Approval
And the last stage of packaging factory quality control procedures and best practices is the final inspection. That should be conducted by factories for finished products before shipping. Ensuring that the packaging meets all specifications and is free from any defects before approval. They can set up a process where the finished packaging is reviewed and approved by the quality department before it is sent to the customer or distribution.
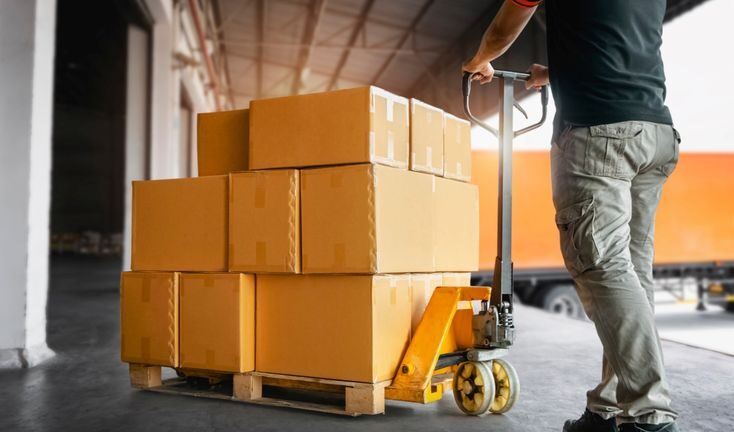
image credit: pinterest
Find quality packaging factories with Maker’s Row
Quality control is an essential factor for packaging. Brands are usually in quest of how packaging factories ensure quality control in production and where to find quality-based packaging factories. This can be seamlessly done with the help of Maker’s Row. It is an online platform that helps brands connect with manufacturers, including those specializing in packaging. It helps to connect brands looking for high-quality production. Here’s how it helps find them
→ Maker’s Row offers an extensive list of manufacturers across various industries, including packaging. Brands can search for factories based on specific requirements, such as materials or packaging type and production capabilities.
→ Maker’s Row allows brands to filter and search factories based on criteria such as location, minimum order quantities, and specific needs. This search helps brands find packaging factories that meet budget and quality standards.
→ Maker’s Row allows manufacturers to showcase their profile and include all important information, such as specifications, portfolios, past work, and even reviews from past clients. This helps brands to compare and find the right factory that meets quality standards.
→ It also provides access to communication directly with factories through the platform. They can discuss how packaging factories ensure quality control in production, custom packaging, request price quotes, and get clarity about lead time and other details. It also offers informative resources such as blogs and videos along with expert advice that helps to understand the packaging solutions and process for both brands and helps packaging factories to grow.
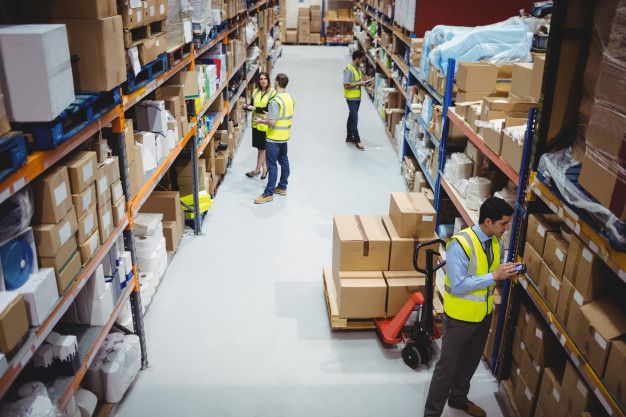
image credit: pinterest
Conclusion
Hence, if packaging factory quality control procedures and best practices are followed, they can consistently enhance their reliability and quality of products. An effective quality control system not only reduces defects and costs but also helps to boost customer satisfaction with how packaging factories ensure quality control in production. Manufacturers are able to produce quality-based packaging products that are durable. Thus enhancing the look and feel of packaging along with quality assurance. This helps in increasing the credibility of packaging factories and helps to attract new clients as well.
You Can Also Read..