Are you the owner of a packing plant and wish to ease out the procedure and enhance the output? Not sure about how to streamline packaging factory workflows, decrease waste, and improve productivity? Finally, lean manufacturing will further ensure that packaging factories remain competitive.
Lean manufacturing—waste elimination through continuous improvement. It integrates processes, lowers expenses, and progresses sustainability efforts in packaging industries. Utilizing platforms such as Maker’s Row can also help simplify this process by connecting factories with trusted, vetted partners and resources to help streamline production workflows.
In this blog, we will talk about a few lean manufacturing techniques implemented in packaging factories, their usefulness, and how Maker’s Row can help you execute them.
What is lean manufacturing?
Lean manufacturing is a waste-reduction philosophy that isn’t a go without a little bit of lean. Waste—anything you do or have that does not add value to your final product goes in here. Here all the things that do not add value to the end product—here any process or any resources at all is waste, in other words.
- Value: What clients Actually Want To Buy From You
- Value Stream Mapping: Look at how value flows through a process and find the waste.
- Movement: Process Flow Principles: make sure that each phase of production moves to the next phase smoothly.
- Pull System UDP: Make to demand or eliminate overproduction.
- Kaizen (Continuous Improvement): An iterative process that evaluates the same processes for incremental improvements.
Companies can drastically change the way they operate with lean techniques, and packaging factory workflows are no exception.
5 Advantages of Lean Manufacturing for your Packaging Factories
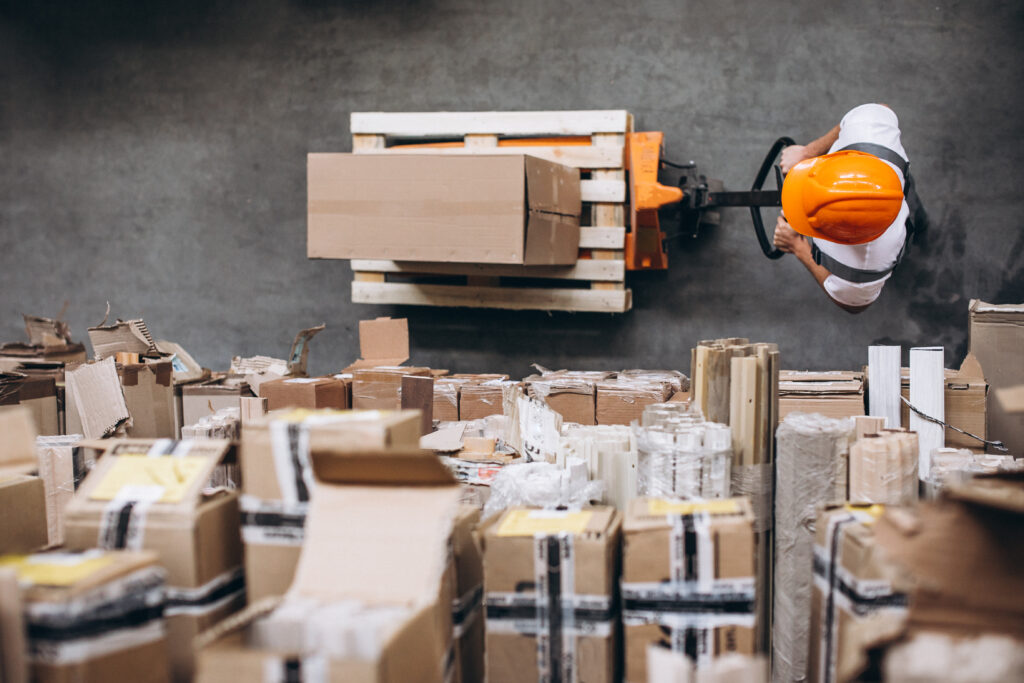
source of picture : Freepik
1. Increased Efficiency
Factories achieve this by making time a reduced variable and increasing productivity, helping to drive down deadlines.
-
Cost Reduction
By eliminating waste, you decrease material, energy, and labour costs and therefore increase profit margins.
-
Improved Product Quality
The lean methods focus more on precision, which leads to fewer defects and enhanced packaging quality
-
Enhanced Sustainability
Lean manufacturing facilitates sustainability by reducing the waste of material and energy.
-
Better Employee Engagement
Rather, free up degrees of freedom for each player to notice and address their own inefficiencies.
Common Challenges in Packaging Factory Workflows
- Firm challenges: There are some problems that do not let productivity happen before lean manufacturing is implemented:
- Overproduction: This is when too many goods are produced, leading to waste of resources as well as storage costs.
- Tedious Layoutst: Production line structures are an inappropriate configuration that causes squandered hours and advancement and update.
- Quality defects: mistakes in the production process that cause rework and material waste.
- Changing Demand: This leads to inefficient workflows, as order volumes can vary widely.
- Communication: Difficulties in communication among teams are a critical issue as it may lead too disruption in production estimation.
This is where lean manufacturing techniques for packaging factories save the day by creating streamlined and adaptable workflows.
Critical Lean Manufacturing Methods for Packaging factory workflows
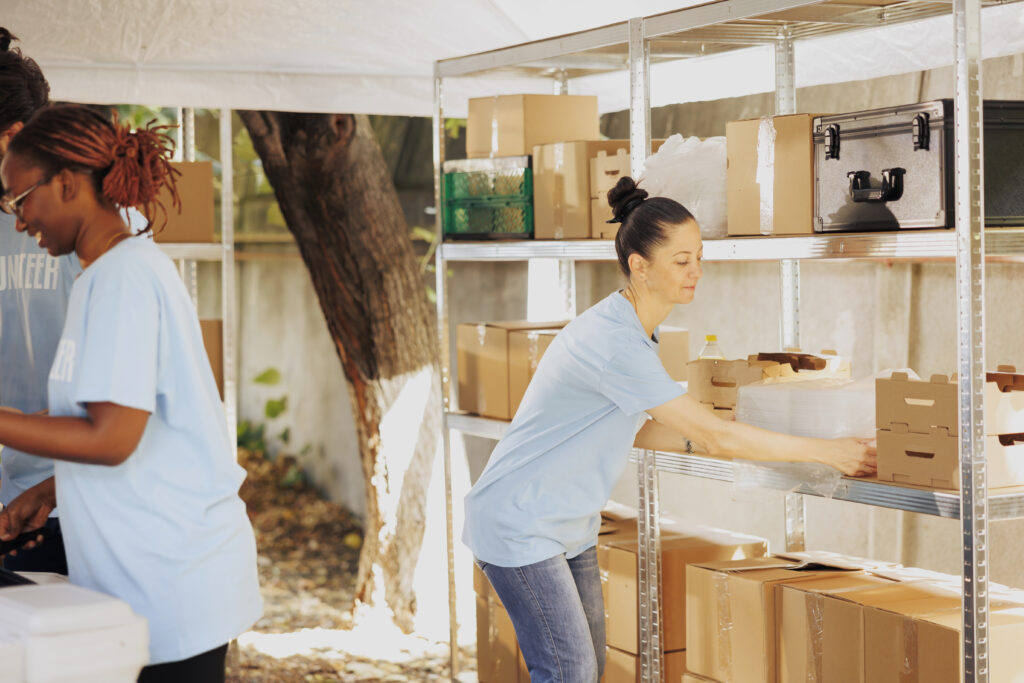
source of picture : Freepik
-
Value Stream Mapping
Take a comprehensive view of the whole production—to identify bottlenecks and wasteful steps. Do the right thing.
-
Just-In-Time (JIT) Production
Make just enough, just in time. JIT reduces waste, thereby minimizing holding costs.
-
5S Methodology
Working safely and efficiently in the workplace can be achieved using the 5S methods, that is, sort, set in order, shine, standardize, and sustain.
-
Total Productive Maintenance (TPM)
Proactive maintenance of equipment reduces downtime and allows for uniform production quality.
-
Cellular Manufacturing
Group the similar tasks together in work cells to create better flow and eliminate unnecessary movement.
-
Continuous improvement (Kaizen)
Create a culture of innovation: Give your employees the power to propose and implement improvements.
-
Tech Automation and Integration
Use automation solutions to do repetitive tasks, and then use advanced tools to monitor the packaging factory workflows in real time.
-
Kanban System
Use a Kanban board to visualize work to prevent overproduction and enable fluid transitions between work items.
How to Implement Lean Manufacturing in Packaging Factories
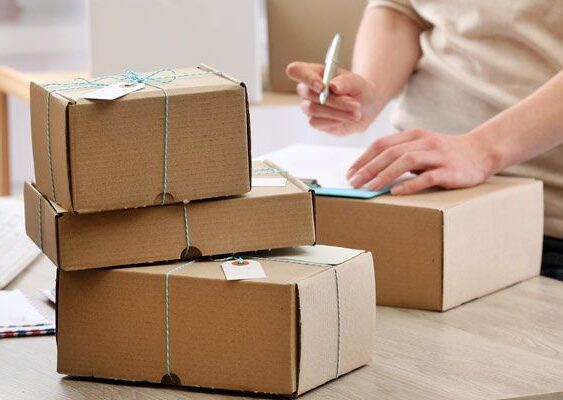
image credit: pinterest
Stage 1: Assess Workflows as it Currently Stand
Review current Packaging factory workflows for improvement opportunities
Step 2: Set Clear Goals
Establish clear, measurable targets, like reductions in cycle time or defect rates.
Step 3: Train Employees
They will also receive regular training and support to continue to apply lean principles and techniques.
Step 4: Start Small
Take small steps—test drive lean tools within pilot projects before deploying them across the factory.
Step 5: Monitor Progress
Data and metrics can be used to monitor the progress of others and identify the potential touchpoints for improvement.
Step 6: Foster a Lean Culture
Foster a culture of continuous improvement—recognize innovative and cooperative internal ideas.
How to Utilize Maker’s Row
Maker’s Row makes it easy to utilize lean manufacturing in your packaging facility by linking you to the people you can rely on for the support and expertise necessary to implement lean manufacturing solutions.
-
Access to Trusted Suppliers
It also makes sure to rely on suppliers with good-quality materials and services to complement the lean initiatives taken.
-
Streamlined Sourcing
With services that allow you to source materials effectively and reduce waste, Maker’s Row also helps optimize your packaging factory workflows.
-
Educational Resources
All so you understand how lean manufacturing can best be implemented.
-
Sustainability Focus
Maker’s Row also focuses on green solutions, allowing you to combine lean practices with sustainability goals.
-
Customized Solutions
Work with industry experts to customize lean tactics that best suit your factory’s unique requirements.
Packaging factories can use Maker’s Row and get faster on the way to lean efficiency and greater productivity.
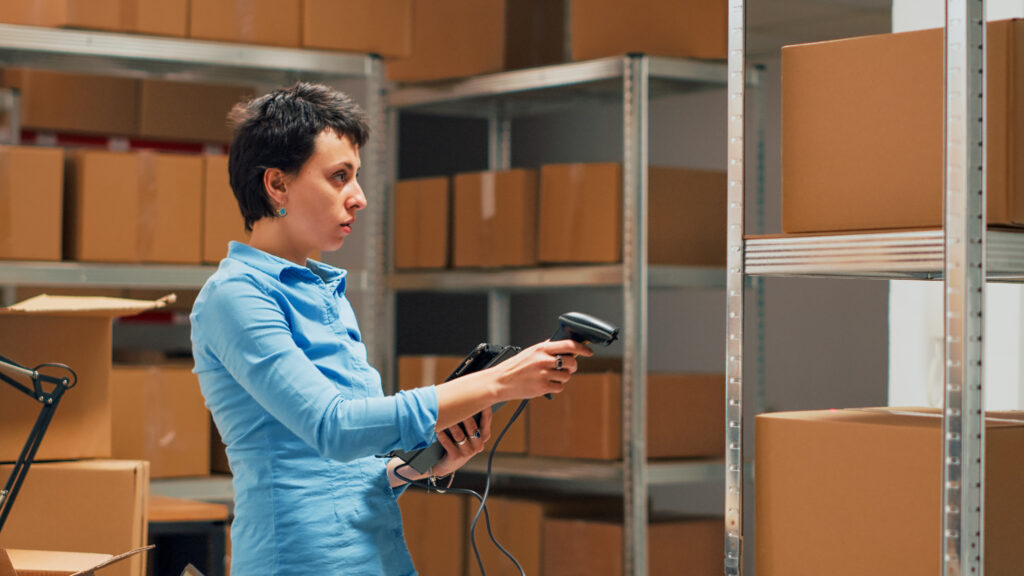
source of picture : Freepik
Conclusion
Lean Manufacturing: This is the Key to Your Success
Packaging factories need to adopt such lean manufacturing techniques if they want to thrive in a highly competitive market (and at a time when cost optimization is almost a part of growth and sustainability, as a debate is). That can make work more efficient, higher-quality, and beneficial for workers and customers.
Maker’s Row, for example, is a tool to help make such a transition, offering the tools and resources needed for your lean manufacturing process.
Just start and accelerate your packaging factory workflows to become an operational excellence practitioner!
Looking for more insights? Check these out!